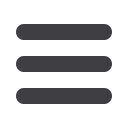

NEWS IN BRIEF
PUBLIC COMMENT –
PLANT CODE OF PRACTICE
In early June, SafeWork Australia
was seeking comment on the Plant
Code of Practice draft. Members were
encouraged to view the draft Code and
use the public comment form. The Code
involves “Safe Design, Manufacture,
Input and Supply of Plant”. The
response deadline was June 22, 2012.
The Draft Code raised issues that are
requirements for hirers and lessors of
plant, suppliers of second hand plant as
well as importers and suppliers of plant
in general. The EWPA raised areas of
concern through the ACCI and members
were encouraged to get involved.
‘HOIST ER’D WITH THEIR
OWN PETARD
In an interesting aside, a recent email
communication from the good people
at Forkforce Australia offered this piece
of industry trivia. Hyster began making
winches and lifting machines for the US
timber industry, and their name actually
originated from the call of labourers
who shouted “hoist ‘er” when a log was
ready to be lifted.
TRAINING UPDATE
The new EWPA Yellow Card Unit of
Competency training program was
launched on May 3, 2012 at the HRIA
Convention on the Gold Coast and will
be introduced to Accredited Trainers
this year. Stage 1 will be introduced
before the end of 2012, Stage 2 will
be the process of ironing out any flaws
and Stage 3 will be the “Statements
of Attainment.” There will be a new
“upgrade training” program to bring
applicants up to date with their skills
level. This will apply to those with older
Yellow Cards. A photo ID system will
be introduced with the final stage being
the introduction of a renewal period
possibly of five years.
TELESCOPIC HANDLERS
The Telescopic Handler Association is
now up and running and progress is
being made on the Annual Inspection
Checklist. The second meeting of the
TSHA was held at the HRIA Convention
with another meeting recently that was
well attended and productive. An annual
inspection checklist is in its final draft
stages and this is aimed at
complimenting the manufacturers’
checklist, or being a useful stand-alone
checklist at the front line level.
30 | ACCESS
in
ACTION | AUGUST 2012
ACCESS in ACTION
Information about Genie
parts and availability is now
more accessible with the launch
of the new Genie Parts Portal.
The new Parts Portal was
conceived by Genie’s National
Parts Manager, Michael
Carmody in September last
year. He could see how much
time was being taken up by
Genie customers asking basic
parts questions, regarding parts
availability and price.
By logging-on through
a password protected link,
customers have access to the
Genie parts inventory where
parts can be identified, their
availability checked and pricing
confirmed.
The Genie Parts Portal has
been progressively made
available to the customer
base. Almost 40 customers
have registered, covering both
Australia and New Zealand.
The new system also allows
Genie staff to log on via their
Manitou’s new 28m
telescopic access platform
received the 2012 Product
of the Year Award at the
IAPA (International Awards
for Powered Access) in the
category of self-propelled
access platforms.
The machine was
commended for its overall
excellence and superior
engineering. The 280TJ and
its 26m version (260TJ) were
unveiled at the Maastricht
APEX show in September 2011.
The TJ articulated platform
boom allows it to get close to
buildings for a better working
zone and increased productivity
while its telescopic jib allows
phone or laptop to access parts
information enabling our field
staff to respond to customers’
questions on the spot.
Calls to the Genie Parts
Department for routine parts
data has dropped by 40%. This
means customers are “being
served” by the online portal
quicker than waiting to talk to
a parts interpreter.
For more information contact
07 3456 4460 or email
Michael.Carmody@terex.com
HR
Launch of online Genie parts portal
In April, New Zealand Labour
Minister Kate Wilkinson told
the construction industry there’s
no longer any excuse for failure
to work safely at height.
The Minister launched the
Best Practice Guidelines for
Working at Height in New
Zealand in Christchurch.
“These guidelines give
everyone in the industry clear,
simple advice that will help
bring down the death and
injury toll from avoidable falls
in the construction industry.
“Falls while working at height
cost this country an estimated
$24 million every year. When
you add in the toll on families,
colleagues and the community,
the situation is unsustainable.”
Ms Wilkinson said it is
important all firms invest in safe
work practices.
“Businesses need to
appreciate the importance of
workplace safety in human cost
and benefits to productivity.
“Studies have shown
organisations that lead the way
in health and safety practices
also tend to have better overall
business performance. Safety is
not a trade-off for productivity;
the two go hand in hand.”
Department of Labour
investigations show more than
50% of falls in construction
NZ guides to reduce workplace falls
while working at height are
from less than three metres.
About 70% of these falls are
from ladders and roofs.
The Best Practice Guidelines
for Working at Height in New
Zealand have been developed
by the Department of Labour in
association with 21 businesses
and industry organisations from
NZ’s construction sector.
The Guidelines are the first in
a series to be published as part
of the Department of Labour’s
three-year harm reduction
campaign ‘Preventing Falls from
Height’. visit: www.beehive.
govt.nz/release/new-guidelines-
reduce-workplace-falls
HR
Manitou wins IAPA Product of Year
it to work in negative or
inaccessible places. Compact
dimensions (width 2.42m x
10.80m - 260TJ; x 11.25 - 280TJ)
optimise maneuverability on
tight sites and transport.
Other features include all-
terrain characteristics
(4 wheel drive); 400kg
capacity basket; and
the 280TJ has two load
capacities, 350kg and 230kg,
depending on the number
of people in the basket (two
or three).
The Kubota, Euro III
A (45hp), engine with
electronic engine speed
management, enables linear
basket translation when the
boom is telescoped. The engine
complies with the European
polluting emission standards
which will apply from 2013.
For more information visit:
www.manitou.com
HR