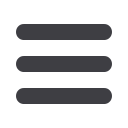

48 | ACCESS
in
ACTION | MAY 2012
ACCESS in ACTION
Figure 1: Cross section of boom with resin
depleted and dry glass areas and location of
cracks.
Monitoring integrity of FRP booms on EWPs
By David Lake,
Advanced Technology Testing and Research
EWPs are designed to permit operator
access to live wires at distances greater than
10 metres above ground. They are easily
manoeuvred into tight places and hence
are used for other operations such as tree
lopping, particularly around power lines.
In the normal course of operations, EWPs
have been used as rests for tree limbs, to lift
power poles or transformers in place, to lift
cross arms and to support cables. None of
which the EWP was designed to do. These
types of application have the potential
for high dynamic loads and have been
known to damage fibreglass reinforced
plastic (FRP) booms. Of course, lifting the
boom without undoing restraining straps
doesn’t do the boom any good either. These
practices can result in cracks in the boom,
either at the external surface or internally.
Poor quality boom manufacturing can
result in significant internal discontinuities
that may also propagate externally or
internally under normal service loading.
Figure 1 shows a defective boom picked
up in a regular acoustic emission (AE) test
program.
External cracks may be detected visually
and this process may be assisted by the
collection of dirt in the crack. Often
cracking occurs only in the external resin
flow coat and may not penetrate into
the underlying fibre composite material.
If it penetrates into the fibre composite
then the integrity of the structure is
compromised. The amount of reduction
in integrity depends upon the depth of
cracking. If detected, repairs should be
undertaken to prevent further cracking
and possible boom failure. How can you
determine if the cracking is only in the flow
coat?
Internal cracking cannot be detected
visually and is best found by conducting an
acoustic emission test of the boom.
To assist in conducting AE tests on
FRP booms, the Australian Standard, AS
4748-2001, Acoustic Emission Testing of
Fiberglass Insulated Booms on Elevating
Work Platforms has been developed.
Prior to the acceptance of AE as a test
method, the recommended procedure for
ensuring structural integrity of EWP’s has
been the application of 1.5 times the SWL
in the most critical position. More recently
that load has been reduced to 1.25 times
Rated Load.
Of course if the UTS (Ultimate Tensile
Strength) of a boom has been reduced to
about 3 times SWL by undetected in-service
damage, application of a load of 1.5 times
SWL will cause further damage to the
boom. Under these test conditions the
boom may not fail catastrophically but be
further undetectably weakened so that it is
more likely to fail in service!
Mechanical tests without AE may cause
more problems than they prevent.
ATTAR has been performing AE
monitoring of the FRP section of EWPs for
over 25 years.
The results of these tests have been
collated and are summarised in Table 1.
It is clear some booms are defective; 1%
contained defects that gave a significant
reduction in strength as indicated by AE.
Most, but not all defective booms were
repairable and re-testing showed the boom
to be satisfactory, thus costly replacement
was avoided.
Booms Tested
3803
Unsatisfactory Booms
45
Satisfactory
423
Defects Reported
- Hydraulic
663
- Other Damage
691
The AE test has also indicated areas
of minor damage, reported as OTHER
DAMAGE, such as gouges, cracks in
flow-coat, cracks in leveling rod support
bar holes and at inspection holes, as well
as looseness between the FRP and steel
sections. These defects and any leakage in
the hydraulic system are always reported.
The suggested re-testing intervals for
satisfactory booms, based on our current
level of knowledge and experience, are as
follows:
1. Booms involved in accidents - retest
immediately after accident to determine
feasibility of repairs as indicated in AS
2550.10.
2. Booms giving very low, no or very high
AE - retest after 12 months.
3. Booms with high damage potential, i.e.
booms used for tree lopping, replacement
of poles, transformers, cross arms or
conductors, and demonstration of
abseiling techniques - retest after
12 months to 24 months.
4. Booms dedicated to light globe
replacement, painting and cleaning -
retest every 4 to 5 years.
Sources of AE from fibre composites
The sources of AE are directly related to
the damage mechanisms that occur in fibre
composites.
These may be broken down into three
groups as follows:
A. Crack breaking matrix only
1. Transverse cracking
2. Splitting
3. Delamination
B. Fibres breaking
4. Fibre break (single)
5. Fibre breaks (multiple)
C. Complex/combination mechanisms
6. Fibre breakage (multiple) with resin
cracking,
Fibre pull out and potential friction
sources. Each mechanism is illustrated in the
figure 2.
The AE characteristics of composites like
FRP are:
1. Large amounts of AE
2. Large increase in activity (AE rate) before
failure
3. At higher stress levels, emission continues
during load holds
4. Felicity effect is a good indicator of prior
damage
5. Rich, informative amplitude distributions
6. Friction at damaged surfaces
is a major AE source, as well as new
damage
As a result of these characteristics, AE
is widely considered “the most” effective
NDT method for assuring the structural
integrity of composite material fabrications,
particularly the glass fibre booms on
elevating work platform vehicles. Its
main advantage over conventional non-
destructive testing techniques is it is not
continued on page 50...