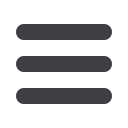
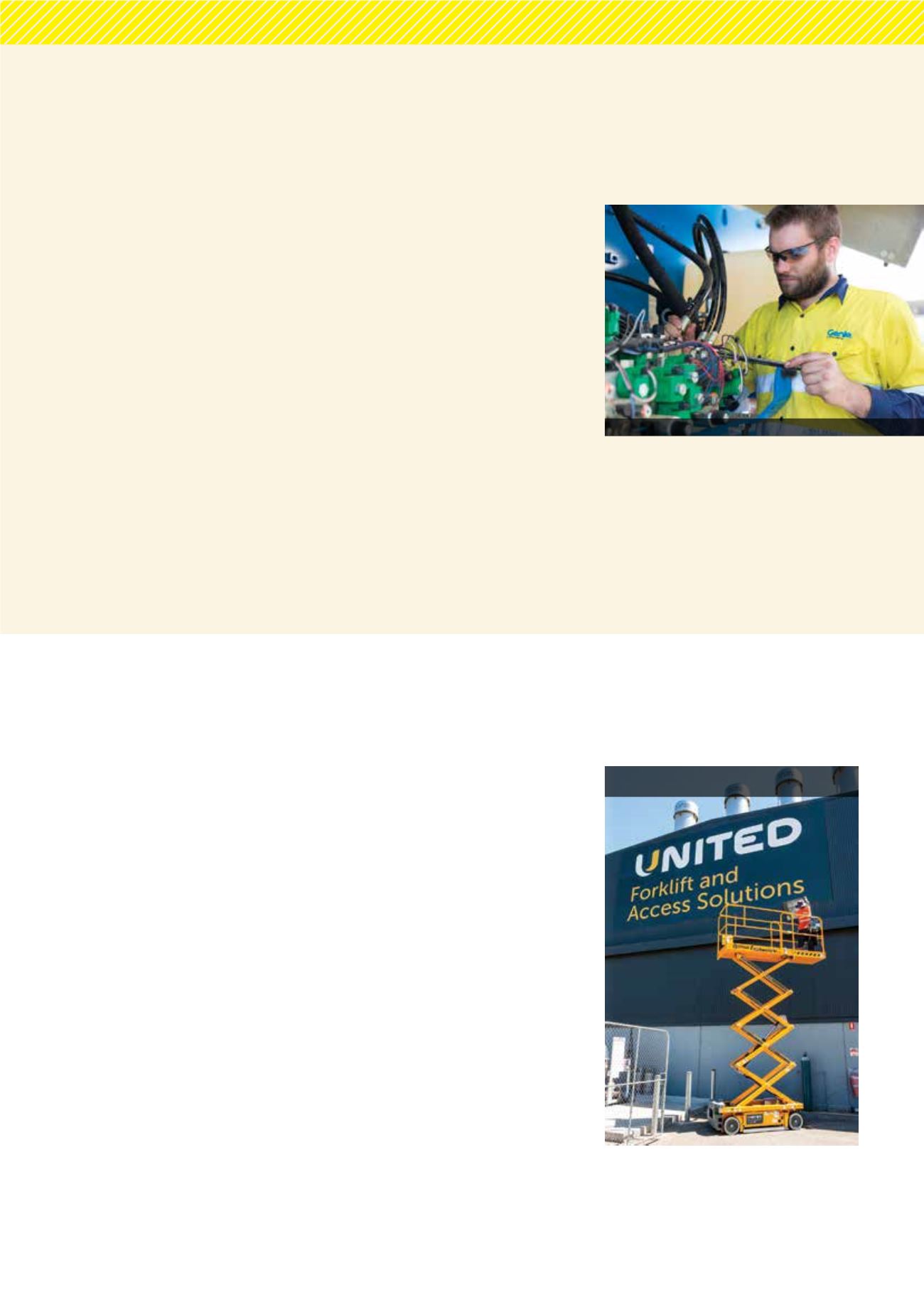
40
ACCESS IN ACTION • NOVEMBER 2016
The 2016 model Optimum 8s, with a
forward speed of 5km/h, 1.5m turning
radius and integrated safety features, are
backed by United Forklift and Access
Solutions’ nationwide service and support
network.
Optimum 8’s asynchronous AC motors
facilitate smooth precision movements in
difficult-to-access places, while ensuring
the safety of its operators and clean,
green, operation. Its narrow turning
radius means operators can manoeuvre in
restricted spaces.
“Optimum 8 is swift and sure-footed
to ensure optimal productivity with its
working height of 7.7m and drivability
at full height up to its platform height
of 5.77m. Its smooth load elevation
and driving, with even, proportional
movements, from the AC motors, translate
into on-the-job comfort, confidence and
safety for operators,” United’s National
Access Product Manager, Andrew
MacDonald said.
Optimum 8 features include: compact
dimensions (0.79m width, 1.9m length)
Optimum 8 electric scissor lift safety features
include an intelligent counterweight design
Electric scissor lifts offer extraordinary access with productivity
Haulotte’s Optimum 8 electric scissor lifts available from United Forklift and
Access Solutions offer economical 24/7 performance inside and outside, with
manoeuvrability and 230kg lift capacity.
will get through standard doors without
needing to use folding guardrails; optimal
weight and configuration to allow
operation in winds up to 45kmh while
maintaining full load capacity; automatic
protection against pot holes and ability to
traverse obstacles; plus can mount truck
ramps while being transported; intelligent
counterweight design in the back of
the chassis; counterweight integrates
protected non-skid steps and storage
area for charger plugs and optional
electrical plugs; hydraulic hoses halved
(from 10 to 5) and hydraulic cylinders
reduced from four to three; maintenance-
free AC motors with no carbon brushes
to be replaced; extra protection against
weather corrosion for pins, screws, bolts
and paint, complemented by waterproof
connectors to safeguard electrical circuits
against humidity and corrosion.
Haulotte ACTIV’Screen embedded
diagnostic device is easy to operate
and provides key information including
tilt, overload, breakdown, necessary
maintenance and battery level. The
system enables technicians to program,
repair, calibrate and control the machine
without other tools.
Contact: 131 607 or visit website:
www.unitedequipment.com.au
ACCESS in ACTION
“Genie 360 Support takes care of every
aspect of our customer’s AWP needs
from initial sales and service through to
technical support, operator training, and
maintenance,” Mitch Ely, Genie National
Operations Manager, Terex AWP said.
“By carefully scrutinising the
maintenance criteria on Genie machines,
analysing their operating histories,
warranty data, customer feedback,
design criteria and overall performance
of a particular machine class, we have
reduced our maintenance requirements.
“These schedule amendments will save
money for our customers, slash down
time in the workshop and generate more
productivity, which is what Genie 360
Support is all about.
“For example, 250 hours was a standard
trigger for an engine service for all
Genie elevated work platforms. After
Genie maintenance schedules slash costs by up to 30%
Genie Australia has introduced a raft of consolidated maintenance protocols, as part of its
Genie 360 Support program that will potentially reduce the maintenance costs of a Genie
scissor or boom lift by up to 30%.
reviewing engine performance data, we
were comfortable with extending this
service interval out to 500 hours. For
customers with large Genie fleets, return
on investment will be increased due to
less parts expenditure and improved
utilisation.”
Similarly, the requirement for hydraulic
oil replacement was every two years, a
procedure which can be costly for rental
companies. Under the new schedule,
Genie is recommending the replacement
of hydraulic oil only as required.
“Likewise some of our products operate
reduction hubs in the wheels. Previously,
the reduction hub oil was changed
annually. Now it’s changed every two
years,” he said.
“By extending certain parts of our
maintenance schedules, we are reducing
maintenance running costs by up to
30% and reducing hours off the time the
machines are out of action in workshops.”
As part of the ongoing AWP leader’s
commitment to continuous improvement,
Genie separated the maintenance
requirements from the service manuals
and consolidated these into one
maintenance manual for boom and
scissors respectively, Mitch said.
Visit: www.terex.com
Genie has reduced maintenance requirements