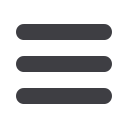
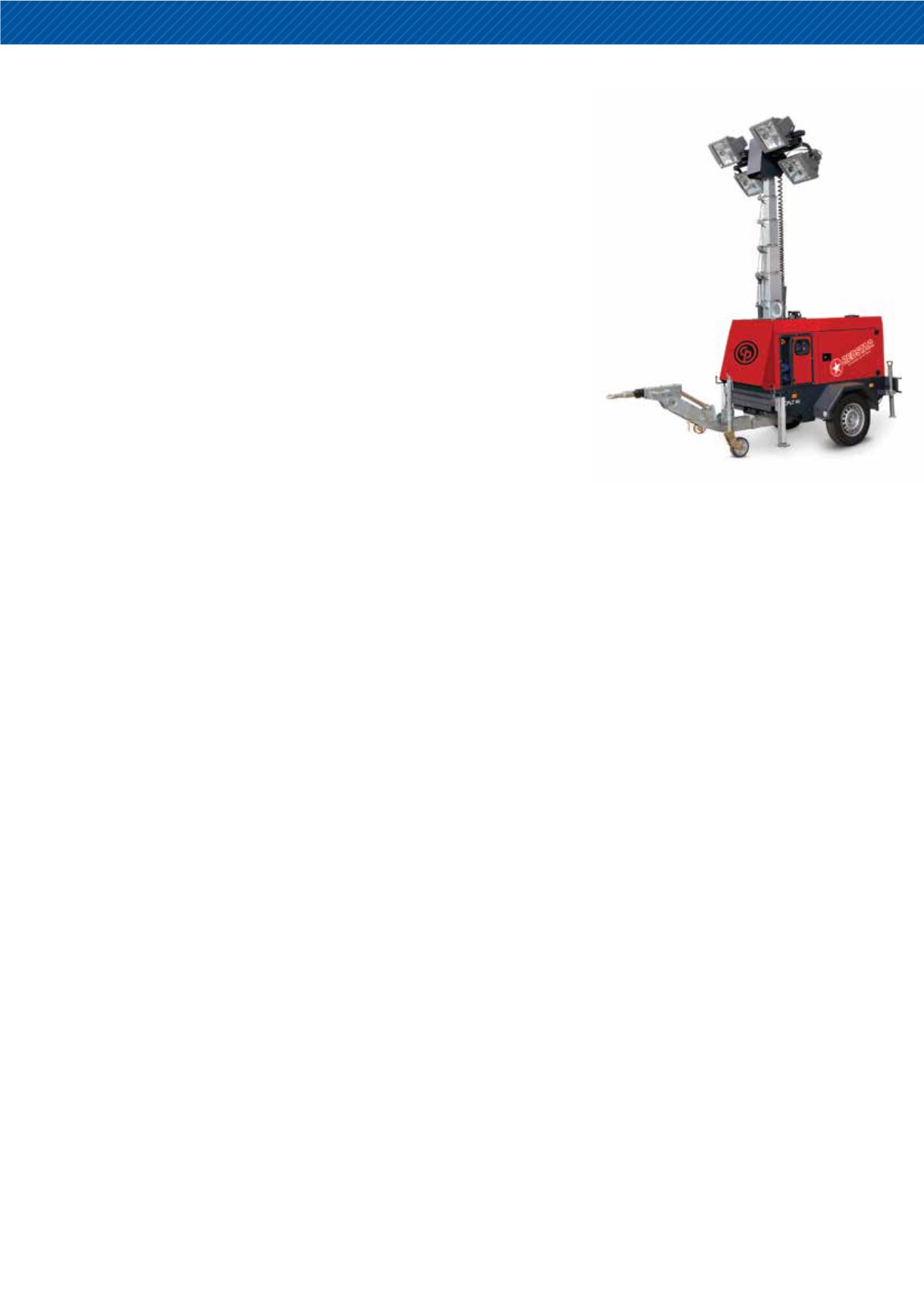
24
HIRE AND RENTAL NEWS • NOVEMBER 2014
GENERATORS, PUMPS & COMPRESSORS
According to Kevin Ennis at Redstar,
lighting towers have become an important
means of ensuring night time work can
be conducted in a safe and efficient way.
Selecting the right lighting tower for your
application is also important.
“If the lighting tower breaks down, or
needs to be taken out of action, there
can be an adverse impact on safety and
productivity,” Kevin said.
“Fortunately, lighting towers are not new
in the market and most of the issues
impacting on reliability and maintenance
are well known.Consider these factors
when selecting a metro & light
construction lighting tower:
Lamp Start-up
One of the biggest causes of lighting tower
breakdowns is when an operator tries to
start all the lights at the same time. This
causes the alternator or capacitors to
be overloaded and can cause expensive
damage to the product. Ask the supplier
for a lighting tower with a controller that
only allows the lights to start one at a time
and avoid overload.
Mast Wear
Hydraulic vertical masts are the most
common arrangement on lighting towers.
They are compact and easy to use but
can suffer wear between the different
telescopic sections. This aided by
corrosion, often leads to the mast getting
stuck. A well designed lighting tower will
have replaceable anti-wear guides in place
to reduce wear and minimise the risk of
the mast getting stuck.
Ballast Control
Ballast is commonly used on lighting
towers to control the flow of current
through the lamps during start-up. Once
the lights are powered up the ballast is no
longer required however in most lighting
towers they remain on. This often leads to
flickering (stroboscopic effect) of the lights
and often reduced lifespan of the lamps
and ballast. Check to ensure electronic
ballasts are used to prevent flickering of
the lights and extended lamp life.
Component Access
A popular trend in lighting towers was to
develop very compact products, enabling
more units to be transported in a single
load. The aim was to reduce transport
costs however the impact was actually
a significant increase in repair and
maintenance costs due to very limited
access to components. A well designed
lighting tower will have adequate access
to all the service and repair components
without having to remove the canopy.
Specifically check for ballast and alternator
access because these can take a lot of
time to access on some designs.
Excess Auxiliary Power
Lighting towers are meant to provide safe
lighting but a trend has developed where
many lighting towers are also fitted with
auxiliary power outlet sockets for other
loads on site. Though this seems like a cost
effective idea, these external auxiliary
loads often cause the lighting tower to
break down due to alternator overload and
other load induced factors. Use the lighting
tower for its intended purpose. Check
auxiliary power outlets on the lighting
tower are within the alternator load limits
or ask for the outlets to be removed.
Parts Identification
One of the first items to go missing from
a new product is the operator’s manual
and parts book. When it comes time to
order spare parts for maintenance, the
owner often uses the internet to search
for the parts. Invariably the wrong part
number of selected (most parts books are
serial number linked), the part does not
fit when it arrives and a great deal of time
and money is lost as a result. Check the
relevant part numbers for maintenance
parts, lubricants and coolants are labeled
on the lighting tower for easy access.
Wind Rating
High winds can cause havoc with a
lighting tower when the mast is fully
erected. Check with your supplier on the
wind rating of the lighting tower.
Automatic Mast Lowering
An easy mistake is for an operator to
attempt to tow the lighting tower away
from the work site without lowering
the mast. Check a handbrake safety
mechanism is fitted that automatically
lowers the mast when the handbrake is
lowered for towing.
Spillage-free base frame
We should always consider the
environment when it comes to product
selection and liquid spillage is often
the biggest threat. An oil leak or a burst
coolant hose can lead to significant
environmental spillage on a work site, not
to mention lost time in productivity.
Check the lighting tower you choose has
an integrated spillage free base frame
design to catch 110% of the on board
liquids in case of a leak or failure.
Stability while being towed
Metro lighting towers often get towed
behind a vehicle to and from work sites.
The maximum towing speeds and stability
of the lighting tower under-carriage are
important factors in avoiding an accidental
roll over going around tight corners or
speed bumps. Your supplier should advise
the maximum safe towing speed for the
lighting tower and also the types of road
surfaces it has been designed for. A torsion
bar type under-carriage, with a low centre
of gravity, should positively contribute to
the metro lighting tower stability.
LED vs Metal Halide Lights
There are pros and cons between LED and
metal halide lights. LED lights are more
robust and consume less power than metal
halide lights. Metal halide lights are much
less expensive and are well proven in this
application. Ultimately the decision will
come down to needs and budget.
Brand & Product Support
Ensure your supplier is offering you a
reputable product, preferably a globally
recognised brand, with local support for
maintenance and repairs from an officially
authorised distributor.
Contact Redstar Equipment
on: 1800 733 782 or visit:
www.redstarequipment.com.auTECH
TALK
How to select the best metro lighting tower