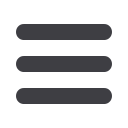

associated with installing a mobile
weighbridge. After considering our options,
we fitted Loadrite scales to our fleet of
Komatsu WA500 and WA480 loaders which
were used on site to fill the trucks with
various materials.
“The use of Loadrite loader scales helped
to reduce the set-up costs for the project,
and increased productivity by ensuring each
truck was carrying the optimum weight
at any one time. Given we were loading
MAY 2012 | HIRE
AND
RENTAL
NEWS
| 77
EQUIPMENT SHOWCASE
On-board weighing systems for wheel
loaders can dramatically improve efficiency
while reducing costs, especially for
projects that would otherwise require
the installation of a mobile weighbridge,
according to an earthmoving and civil
construction company.
Road and earthworks contracting
company, SEE Civil, estimates it has made
significant savings thanks to the installation
of Loadrite’s on-board weighing system on
its fleet of Komatsu loaders. The Loadrite
L-2180 is designed to provide accurate and
consistent results direct from the loader.
With on-board weighing, the system helps
operators avoid costly overloading, without
the need for a weighbridge.
SEE Civil’s Operations Manager, Ross
Smith, said the company introduced the
L-2180 two years ago to avoid having to
install a mobile weighbridge at a leased
quarry near a job site in northern NSW.
“We were contracted to supply and
deliver all the pavement materials for the
$40 million Alstonville bypass project,” Ross
said. “The project called for a specific road
base called chert, believed to be a superior
material because it holds together better
than some alternative road bases.”
The company found a chert resource
in a quarry at Wardell, 30kms away from
the job site. It leased the quarry and set
up a mobile crushing and screening plant.
During the course of the 12 month project,
300,000 tonnes of material were loaded to
enable completion of the bypass.
“Because we were only leasing the
quarry, we wanted to avoid the costs
Loader scales deliver cost savings
Since installing Loadrite’s on-board weighing
system on its Komatsu loaders, SEE Civil has made
significant cost savings
over 100 32-tonne trucks daily with up to
nine various materials ranging from top
and bottom course road base to drainage
aggregates of varying sizes and drainage
blanket materials, Loadrite played an
integral role in the success of the project,”
Ross said.
By installing software to transmit Loadrite
data directly to MYOB, Ross was able to
reduce the time spent on inputting the data
for invoicing.
“Our invoices are calculated according
to the type of material, weight and
destination. Loadrite scales capture all of
this data on site when each load is weighed.
We were loading 100 trucks a day, which
meant there was a lot of data that needed
to be inputted on a daily basis,” Ross said.
The process works via a wireless internet
connection. Information captured via
the Loadrite scale including the type
of material, weight and destination is
exported at the end of each day into an
offsite database program. This database
integrates with MYOB to generate invoices
as required.
“We’ve got six major projects underway
across NSW and Queensland and Loadrite
systems are either being used, or soon will
be, across all sites,” Ross said.
“It’s easy for loader operators to use
and due to the fact the software adjusts
automatically throughout the day to cope
with temperature changes that can affect
weighing performance, we’re confident of
ensuring accurate weights every time.”
For more contact: 09 820 7736 or visit:
www.loadritescales.com
HR