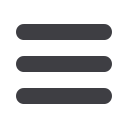
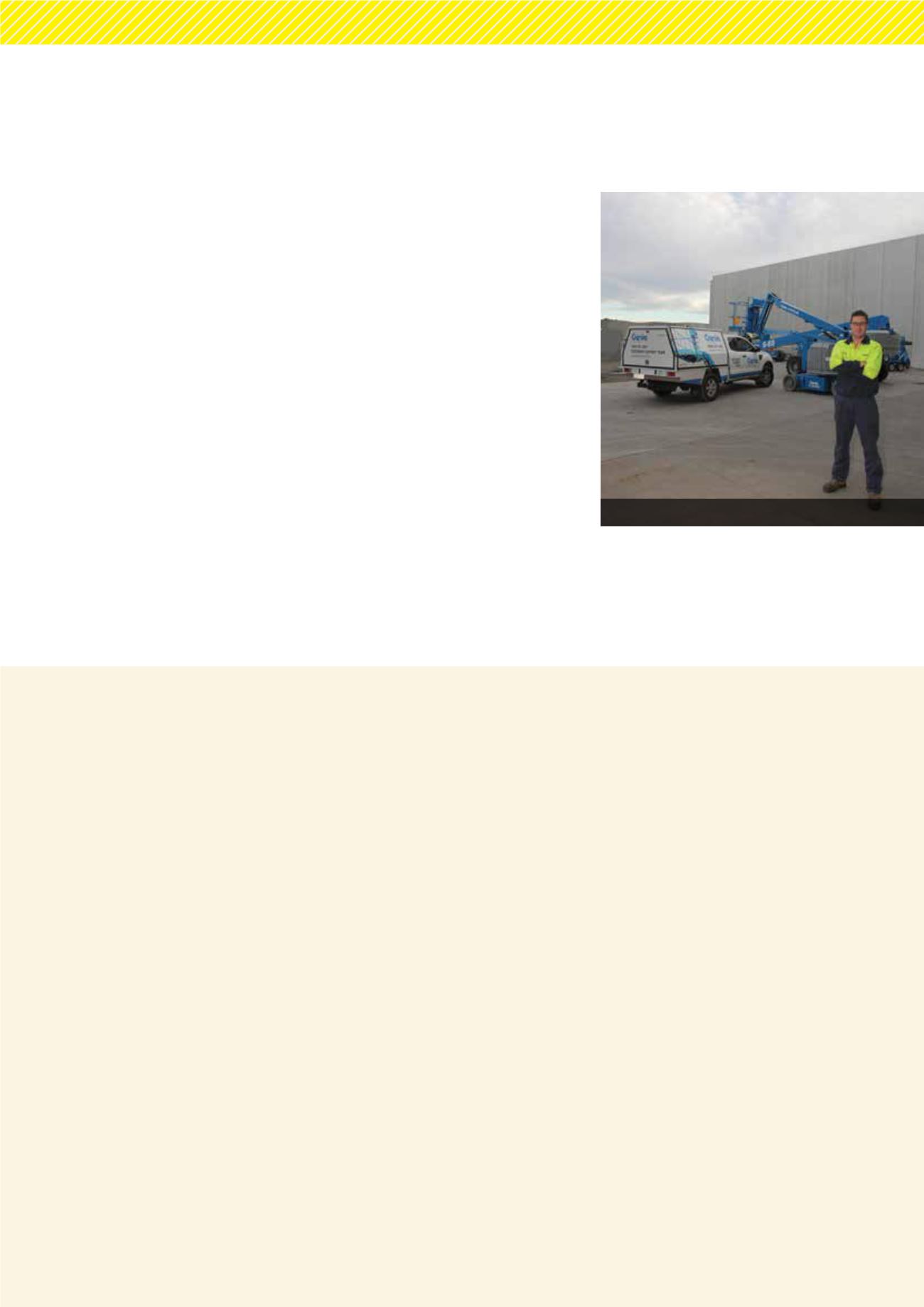
ACCESS in ACTION
In a company-wide initiative, Terex has
declared 2014 as the Year of the Service
Technician. Ron DeFeo, Chairman and
CEO of Terex Corporation and Matt Fearon,
President of Terex Aerial Work Platforms
(Genie), are driving a global program
which acknowledges the outstanding
contribution Field Service Technicians
continue to make to the success of the
company and its customers, in Australia
and around the globe.
“Customers rely upon the service
technicians in our organisation to make
our products do what they are supposed to
do,” Ron DeFeo said.
“In 2013, our technical team members in
the field did a great job so we decided to
dedicate 2014 to them in recognition of
their continuing drive and support of the
Genie brand.
“There were many instances where the
Genie technicians went well above and
beyond the call of duty to assist customers.
While many of us feel weekends and
nights are sacrosanct, Genie Field Service
Genie dedicates 2014 to service excellence
Technicians willingly give up their private
time to help and support customers.”
“The focus of the Genie Field Service
Technician is on customer advancement
and improvement,” Brad Lawrence,
General Manager of Genie Australia said.
“Our technical team members are
committed to maintaining Genie
equipment in great condition to support
our customers. Through having the best
aftermarket support service in the industry,
we believe our customers will choose to
purchase Genie access equipment again.”
To launch the year-long program
in Australia, Genie’s Field Service
Technicians from all Australian branches
attended a series of service specific
briefings and presentations on the Gold
Coast. Matt Fearon was in Australia and
participated in the presentation which
coincided with the May launch of the
Genie SX-180 boom lift at the HRIA
Convention, HIRE14.
Matt outlined the global strategy to the
group and the place service holds in
providing the best aftermarket support.
His key message: “Sales sells the first,
but service sells the rest”, left a lasting
impression in the minds of all present.
Contact: 07 3456 4444 or visit:
www.genieindustries.com.auA recent Safety News Alert from the Tutt
Bryant Group relating to an EWP fatality
in Tasmania in 2009 raises issues relevant
to the EWPA’s ongoing battle with non-
compliant machines and the importance of
major inspections.
The EWPA suggests the issues raised in
the safety alert are highlighted to service
teams and operators to help prevent
another occurrence. The following is an
excerpt from the Tutt Bryant Group’s
Safety Alert 17 June 2014.
Glaring defects overlooked in lead up
to death
A worker who neglected to perform a pre-
start check of a dilapidated elevated work
platform (EWP) - because his desire to get
on with the job “overtook him” - is one of
three people whose actions contributed
to the death of a diesel fitter, a coronial
inquiry has found.
Tasmanian Coroner Olivia McTaggart
found even a cursory check would have
revealed deficiencies in the EWP.
In August 2009, contractor Nathan Graham
- a Russell Allport and Co employee - was
preparing to use an EWP to replace a
pipeline at Nyrstar Hobart’s zinc works
when he realised it had engine problems.
He contacted Tasmanian Access Systems,
seeking a replacement EWP, and one
was delivered by Access Systems' diesel
mechanic Christopher WilliamWagg in
less than an hour. Graham then began
operating the EWP without conducting a
visual or functional pre-start check, and
found it accelerated too rapidly, jolted with
abnormally high “revs”, and had a faulty
emergency stop button.
Wagg replaced Graham in the EWP basket
to investigate the problem, and sustained
fatal head injuries when the EWP moved
rapidly towards an overhead walkway,
crushing him between the basket handrail
and a structural beam.
The Coroner found Access Systems’ EWP
had numerous defects, including the
absence of directional decals (which help
operators steer the EWP), an inoperable
emergency stop button and warning horn,
an inoperable “creep speed” function, and
illegible warning signs and instructions in
the basket due to wear and tear.
She also found there were “glaring
omissions” in the machine’s log book,
with no references to a number of required
three-monthly services, and at least 85
hours of operation that weren’t accounted
for. Further, the EWP wasn’t subjected to
a major inspection or overhaul by the end
of its 10th year of service in April 2007, as
required by the relevant Standard.
Three people contributed to the fatal
incident, including the deceased worker,
the Coroner found.
Wagg chose to operate the EWP when
he knew it had been moving erratically,
placing himself in danger," she said.
Graham contributed to Wagg’s death in
failing to detect the defects and put the
EWP out of service, “effectively allowing
Mr Wagg into an inherently dangerous
workplace situation”, the Coroner said.
Gerard Sullivan, a motor mechanic at
Instant Scaffolds responsible for servicing
the EWP contributed to the fatality by
failing to conduct an adequate pre-delivery
check of the EWP, and allowing it to leave
the hire yard, the Coroner found. She
found he identified the missing decals
six months before the incident, but didn’t
replace them, and failed to organise the
10-year major service, which “would have
remedied the defects”.
EWP fatality and the coroner’s report
ACCESS IN ACTION • NOVEMBER 2014
38
Terex has declared 2014 as the Year of the
Service Technician