Coates introduces world’s first recycled plastic traffic barriers
Martin Sinclair Dec 11
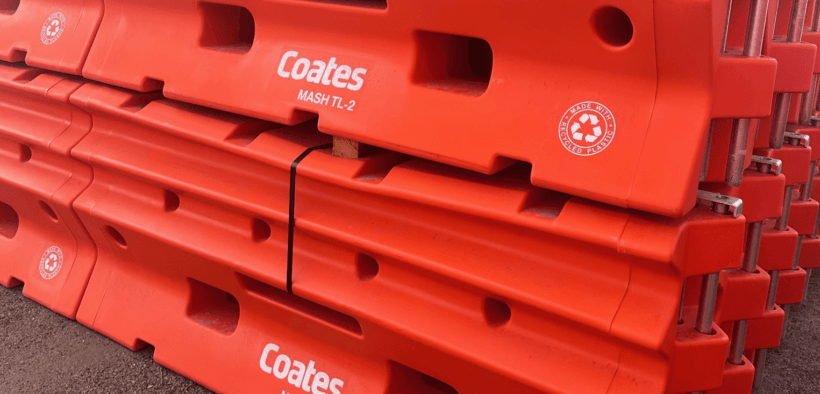
Coates is breathing new life into its end-of-life cycle Armorzone plastic traffic barriers by collaborating with Ingal Civil Products to recycle and reuse the materials to manufacture the world’s first road crash-tested recycled plastic barriers. To date, Coates has recycled more than 10,600 barriers that are no longer compliant with new safety standards and repurposed more than 500 tonnes of high-density polyethylene (HDPE) plastic that could otherwise have gone to landfill.
This initiative not only provides customers with a more sustainable product that meets both the new MASH TL-1 and TL-2 standards for road safety barrier systems, but also helps Coates to deliver on its sustainability strategy and strengthen its commitment to the circular economy.
“As Australia’s road safety standard for traffic barriers has evolved, Coates has pursued sustainable ways to upgrade its fleet of water-filled HDPE barriers,” explains Robyn Simpson, National Manager Environment & Sustainability for Coates. “We began a traffic barrier recycling program in FY22 focused solely on recycling non-compliant and end-of-life plastic barriers.
“Now, we’re excited to partner with our supply chain on this initiative that incorporates 10% recycled materials into the manufacture of new barriers, creating a highly circular fleet. The result is a one-of-a kind MASH-compliant barrier that is durable, recyclable, sustainable and efficient to produce.”
Coates is a Bronze Partner of Sustainability Advantage, the NSW Government’s program that partners with business, industry and government to build capability to drive ambitious and tangible action to reduce emissions, embed circular economy and restore nature. Coates graduated from the program’s inaugural Circular Economy Leadership Accelerator in 2023.
Anne-Marie Poirrier, Director of Sustainability and Circular Economy Partnerships at the NSW Department of Climate Change, Energy, the Environment and Water, says, “We are thrilled to see Coates’ practical application of learnings and engagement with suppliers reflected in higher ambition and action to achieve a circular solution that delivers a more sustainable product to market.”
Taking a more sustainable approach to road safety
Armorzone plastic water-filled barriers are a durable product. Using them in a hire arrangement enhances their circularity, thanks to high utilisation rates. Coates and its supply chain partners are now improving this further by incorporating principles of redesign and recycling.
- End-of-life barriers are consolidated across Coates branches and transported to a recycling facility in Sydney for processing. Metal pins are removed, and the barriers are cut and shredded into 8mm
- The pellets are processed and quality-assured, before being bagged and exported to a rotational moulding material specialist in North Auckland. They undergo further processing and are blended with other materials into a powdered product.
- The powdered blend, containing 10% barrier material from Coates, is then used by a moulded plastic manufacturer to blow-mould new HDPE plastic barriers.
- The barriers are then transported to Australia and sold by Ingal Civil Products. Once in the Coates fleet, they are hired by customers.
Efficient processing
Processing non-compliant barriers locally reduces the volume of product that Coates transports for recycling. “As the plastic barriers feature a large air-filled cavity, shipping each unit in its original form would create almost a 775 m3 load for every 1,000 barriers recycled – that is around twelve containers fully loaded,” says Andre Garrido, National Product Manager for Coates. “Reducing the barriers to pellets eliminates the need to move large volumes of air, minimising the cost and energy required for transportation.”
Durability
The lifespan of plastic traffic barriers adds to the circularity of this product. “This type of barrier is durable and repairable, and in the rental market typically lasts 5-7 years when not subjected to vehicle collisions,” says Andre.
Recyclability
Plastic traffic barriers are made from uniform materials that are easy to separate, making it a product that is highly recyclable. “99% of materials used to manufacture our new fleet of barriers can eventually be recycled or repurposed,” says Andre.
Efficient application
The design of Armorzone MASH TL2 traffic barriers requires almost one-third less water to fill than other plastic barriers. “There are obvious environmental benefits to a reduced water requirement across the lifecycle of this asset; for every 100 Armorzone MASH barriers used, 17,600L of water is saved,” says Andre. “This design also minimises handling issues associated with moving and installing bulky products, as the empty units are also lighter than those of competitors.”
Product innovation
With 10% recycled plastic currently tested and approved for use in the new traffic barriers, Coates and its supply chain partners continue to collaborate in exploring new ways to apply the remaining 90% of surplus recycled material. “It’s been quite interesting investigating ways to use these materials to diversify and improve the circularity of our fleet,” says Andre. “Manufacturing ground protection track mats for major events is one example. We also recently received a recycled plastic kayak from our manufacturer, which is a fun way to showcase the many ways these recycled materials can be repurposed.”
Safety and sustainability assured
In a world-first for the industry, this recycled plastic product has been road crash-tested and approved for use by the Austroads Safety Barrier Assessment Panel (ASBAP). “This means up to 10% recycled materials can be re-used without diminishing the performance or integrity of the barrier in any way,” says Andre. “And with further testing there is potential to increase the amount of recycled material used in the new barriers.”
Coates’ new barriers will also undergo independent verification for an Environmental Product Declaration (EPD), adds Robyn “This declaration will produce transparent and comparable data on the environmental impact of this barrier throughout its lifecycle, making it easier for customers to meet their procurement requirements and to understand the impact of choosing this product,” she says.